What is Porosity in Welding: Common Resources and Reliable Treatments
Unraveling the Secret of Porosity in Welding: Tips for Reducing Defects and Maximizing Quality
In the intricate world of welding, porosity stays a relentless obstacle that can considerably affect the top quality and integrity of bonded joints. Understanding the elements that add to porosity development is crucial in the quest of perfect welds. By untangling the enigma of porosity and implementing reliable techniques for issue reduction, welders can elevate the criteria of their job to achieve remarkable top quality outcomes. As we dig into the depths of porosity in welding, discovering the secrets to its prevention and control will be paramount for professionals seeking to master the art of premium weldments.
Comprehending Porosity in Welding
Porosity in welding, an usual issue experienced by welders, describes the visibility of gas pockets or spaces in the welded material, which can endanger the honesty and quality of the weld. These gas pockets are usually caught throughout the welding procedure due to different aspects such as incorrect shielding gas, infected base products, or inaccurate welding specifications. The formation of porosity can weaken the weld, making it susceptible to cracking and corrosion, inevitably causing structural failings.
By identifying the importance of keeping proper gas protecting, making certain the cleanliness of base products, and maximizing welding settings, welders can dramatically decrease the likelihood of porosity development. Generally, an extensive understanding of porosity in welding is important for welders to generate top notch and resilient welds.
Common Root Causes Of Porosity
When inspecting welding procedures for possible high quality problems, understanding the usual root causes of porosity is essential for preserving weld stability and stopping architectural failures. Porosity, defined by the visibility of cavities or spaces in the weld steel, can dramatically jeopardize the mechanical properties of a welded joint. One common source of porosity is incorrect protecting gas coverage. Inadequate protecting gas flow rates or improper gas mixes can result in atmospheric contamination, leading to porosity development.
Additionally, welding at incorrect specifications, such as excessively high traveling speeds or currents, can generate extreme turbulence in the weld swimming pool, capturing gases and causing porosity. By attending to these usual reasons via proper gas shielding, material preparation, and adherence to optimum welding specifications, welders can reduce porosity and enhance the high quality of their welds.
Methods for Porosity Avoidance
Carrying out reliable preventative measures is essential in reducing the event of porosity in welding processes. One method for porosity avoidance is making sure appropriate cleansing of the base steel before welding. Pollutants such as oil, grease, corrosion, and paint can result in porosity, so thorough cleansing utilizing proper solvents or mechanical techniques is necessary.

Utilizing premium filler products and securing gases that are suitable for the base visit here metal and welding procedure can substantially decrease the threat of porosity. Furthermore, maintaining correct welding specifications, such as voltage, current, take a trip rate, and gas flow price, is crucial for porosity prevention.
In addition, utilizing proper welding strategies, such as keeping a consistent travel speed, electrode angle, and arc length, can aid stop porosity (What is Porosity). Appropriate training of welders to guarantee they adhere to ideal techniques and high quality control procedures is likewise important in minimizing porosity flaws in welding
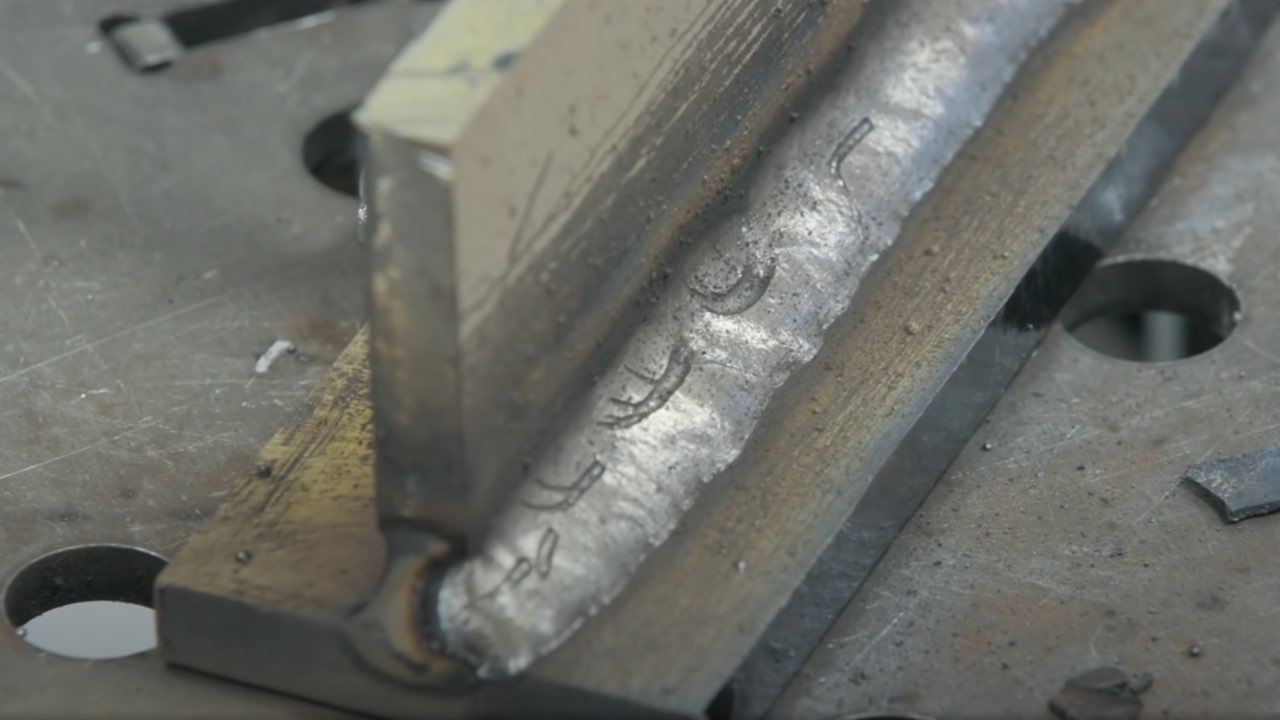
Ideal Practices for High Quality Welds
Ensuring adherence to sector standards and proper weld joint preparation are essential facets of attaining continually top notch welds. Along with these foundational steps, there are several finest techniques that welders can carry out to even more enhance the high quality of their welds. One secret method is preserving proper cleanliness in the welding area. Pollutants such as oil, oil, rust, and paint can adversely influence the high quality of the weld, bring about problems. Extensively cleaning up the work surface and surrounding location before welding can aid alleviate these issues.
One more finest method is to very carefully choose the suitable welding specifications for the particular materials being signed up with. Correct parameter choice ensures optimum weld penetration, fusion, and overall top quality. Making use of top notch welding consumables, such as electrodes and filler steels, can considerably influence the last weld top quality.
Relevance of Porosity Control
Porosity control plays an important duty in guaranteeing the integrity and top quality of welding joints. Porosity, defined by the existence of cavities or voids within the weld metal, can substantially endanger the mechanical residential properties and architectural honesty of the weld. Excessive porosity weakens index the weld, making it more vulnerable to breaking, deterioration, and overall failing under functional tons.
Efficient porosity control is crucial for keeping the preferred mechanical residential properties, such as strength, ductility, and durability, of the welded joint. What is Porosity. By lessening porosity, welders can boost the overall high quality and reliability of the weld, making sure that it fulfills the efficiency demands of the desired application
In addition, porosity control is crucial for attaining the desired aesthetic look of the weld. Excessive porosity not only have a peek here deteriorates the weld but also interferes with its visual charm, which can be essential in industries where appearances are crucial. Proper porosity control methods, such as making use of the appropriate shielding gas, controlling the welding specifications, and guaranteeing correct tidiness of the base products, are vital for generating premium welds with very little flaws.
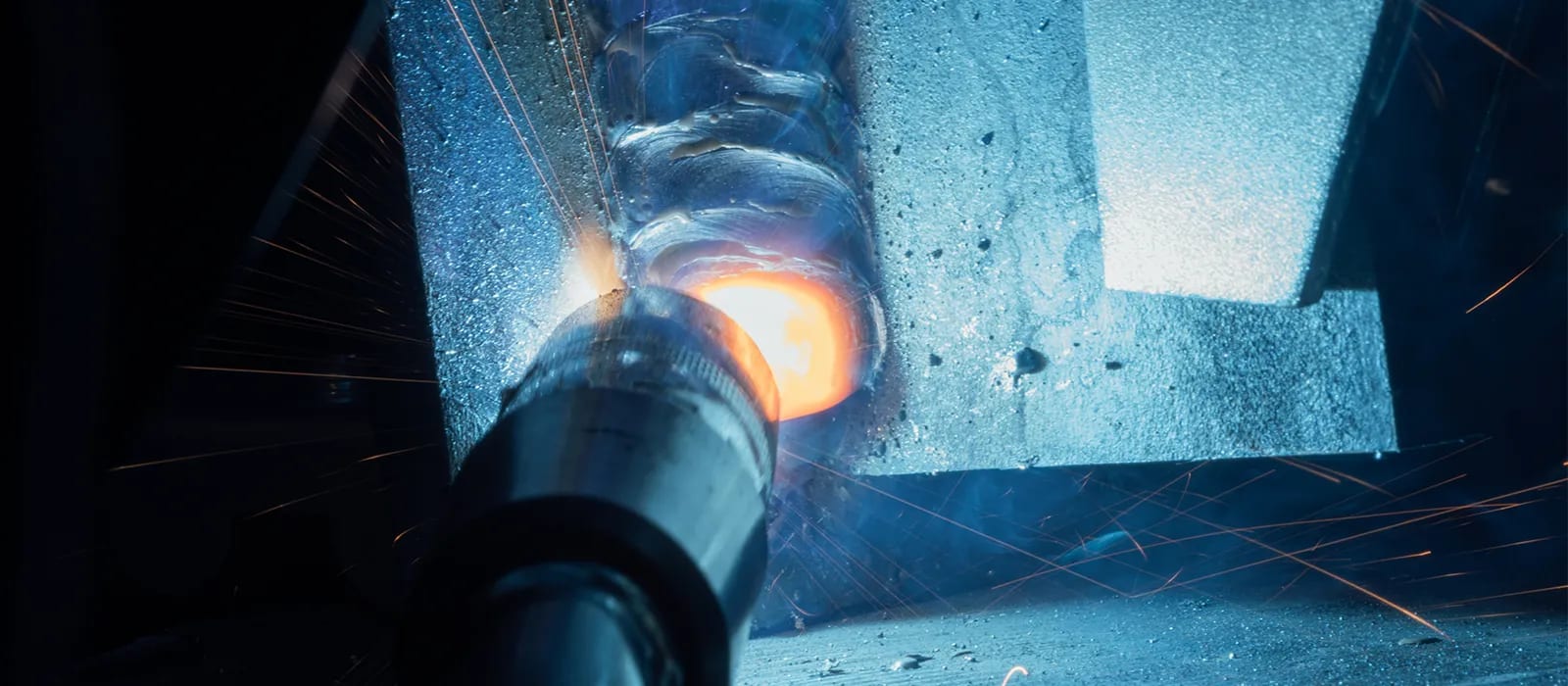
Conclusion
Finally, porosity in welding is a typical defect that can jeopardize the quality of the weld. By recognizing the reasons for porosity and implementing appropriate avoidance strategies, welders can minimize problems and attain better welds. It is important to manage porosity in welding to make certain the integrity and stamina of the end product. Applying best practices for porosity control is important for attaining optimum welding outcomes.